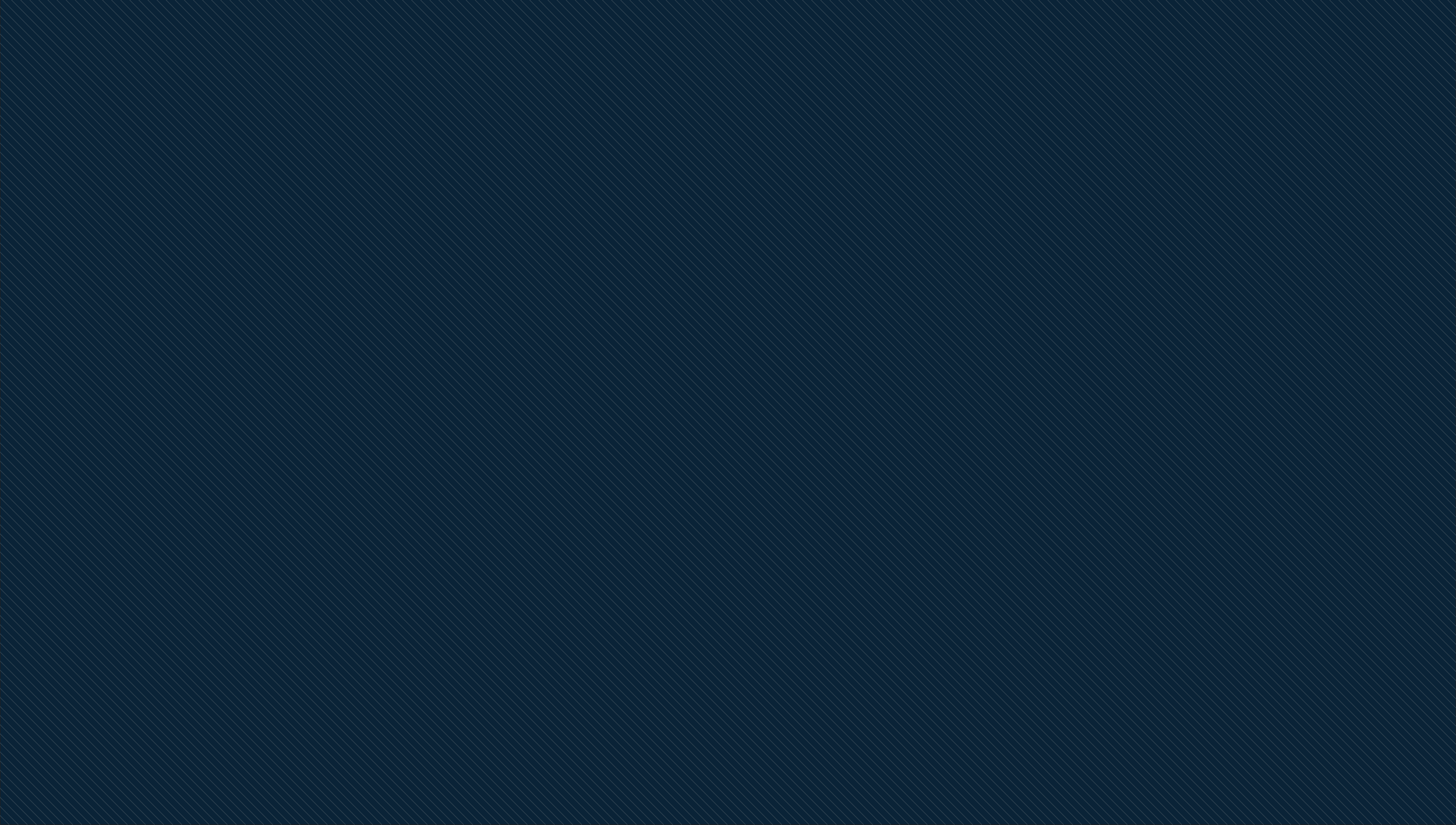
News
How We Made A Fundamentally Better Transmission for Next Generation EVs
Electric vehicle adoption is accelerating at a record pace – nearly 14 million EVs were sold in 2023 (about 18% of all new cars). As the industry scales, automakers face intense pressure to improve range and performance while driving costs down. One often-overlooked opportunity is the transmission: most EVs use a simple single-speed gearbox today, but this “one-size-fits-all” approach forces compromises between acceleration, top speed, and efficiency. Ingear addresses three major gaps in legacy ICE-Age multispeed transmissions…
Two Gears Beat One in EVs—And How Ingear Made It Finally Practical
The Need for Smarter EV Transmissions
Electric vehicle adoption is accelerating at a record pace – nearly 14 million EVs were sold in 2023 (about 18% of all new cars). As the industry scales, automakers face intense pressure to improve range and performance while driving costs down. One often-overlooked opportunity is the transmission: most EVs use a simple single-speed gearbox today, but this “one-size-fits-all” approach forces compromises between acceleration, top speed, and efficiency. Ingear addresses three major gaps in legacy ICE-Age multispeed transmissions by being:
(1) Low cost – it uses proven mechanical technology and common materials rather than expensive exotic components.
(2) High efficiency – its innovative design minimizes energy losses so more battery power translates to vehicle motion and extended range.
(3) Smooth shifting – it shifts gears seamlessly without jolts or pauses in power, preserving the effortless driving feel EV owners expect, while reducing wear on the motor and drivetrain.
We dive deeper on why ICE-age transmission options (traditional multi-speed automatics, dual-clutch gearboxes, CVTs, or the status-quo single-speed) fall short on one or more of these criteria for EVs in our article in “How Transmissions Became A Part Of Every Car, And Why They Will Again In The EV Era”.
In short, Ingear was conceived as the inevitable next step – a transmission designed from the ground up to meet all three needs at once. The result is a patented two-speed system that delivers the efficiency gains of a multi-speed gearbox without the cost, weight, or roughness penalties, making it a game-changer for the EV market.
How Ingear Works: The Engineering Behind the Innovation
A. The Core Transmission Concept
Ingear’s core concept is a purpose-built multi-speed transmission for EVs rather than a repurposed ICE vehicle gearbox. Most EV powertrains today use a fixed reduction gear train (typically totalling around 9:1 ratio) between the motor and wheels. Ingear introduces a second, lower gear ratio for improved launch acceleration and hill climbing, and a higher gear for efficient cruising – but it achieves this with elegant simplicity. Instead of adding bulky gearsets or clutches, Ingear replaces one of the fixed gear stages with a continuous silent chain drive and an innovative morphing sprocket. In essence, the transmission uses a strong chain running over two sprockets (one at the motor output and one at the differential input) to transmit power. By “morphing” the diameter of the output sprocket, the system can switch between a low gear (larger sprocket radius) and high gear (smaller sprocket radius) on the fly. This entire shift mechanism is built in without requiring a traditional clutch or complex multiple gear trains.
Crucially, the Ingear design keeps the architecture lean to avoid the weight and efficiency drawbacks that plagued earlier multi-speed EV attempts. There is no torque converter, no multi-plate clutch pack, no synchros and no high-pressure hydraulic circuit needed to actuate shifts. Instead, a simple solenoid actuator slides the sprocket segments (more on that below) at the precise moment when load on that segment is zero, while the motor controller momentarily adjusts speed to synchronize the shift. Because of this clever timing, shifts complete in under one wheel revolution – in some designs as quick as 19 milliseconds – with virtually no perceptible change in drive torque. The motor never fully “uncouples” from the wheels during a gear change, so the car continues to be pushed smoothly forward even as the ratio changes. This is enabled by what we call our “continuous torque” geometry, meaning the motor’s torque flow to the wheels is never interrupted, even in mid-shift. In practice, the driving experience feels like a single-speed EV – smooth and seamless – except the vehicle gets to leverage a second gear for better performance and efficiency. By designing this system specifically for EV requirements, Ingear maximizes efficiency (only a single gear mesh and a chain are in the power path, with no parasitic drag from idling gears or clutches) and keeps the solution compact. It essentially adds a second gear without adding a full ICE-age gearbox. The result is a transmission that delivers the best of both worlds: multi-speed performance gains with nearly the simplicity, efficiency, and cost of a single-speed drive.
B. Segmented Gear Design
At the heart of Ingear’s innovation is its morphing output sprocket – a segmented gear that can change its effective diameter during a shift. Rather than two separate fixed gears for high and low, Ingear uses one gear built from multiple interlocking segments that slide one at a time to alter the gear ratio. In high-gear mode, these segments retract inward, forming a smaller-radius sprocket. In low-gear mode, the segments extend outward to create a larger-radius sprocket that slows the output relative to the motor for increased torque. During a shift, an actuator pushes a track out to slide one “free” segment at a time into the chain’s path, “assembling” the larger sprocket step by step. Thanks to careful geometry, the chain stays engaged on the smaller-radius portion until the new segment is almost fully in place, so torque continues flowing through the already-engaged part of the sprocket. As the vehicle’s output shaft rotates, five segments move to form the new gear before the shift completes. When downshifting (high to low gear), the first segment to move has a special curved lead-in that smoothly lifts the chain onto the expanding sprocket without any jerk or binding. Likewise, when upshifting, the last segment to retract has a guide that eases the chain back down to the smaller radius. This ingenious segmented approach means the chain never has to derail or jump between sprockets; it always runs in-plane, and the effective gear ratio changes within one rotation of the wheel.
This segmented design enables smooth, reliable shifting with minimal mechanical complexity. It avoids the clutches, synchromesh, or heavy gearing found in traditional transmissions, making it well-suited for efficient mass production using standard materials and processes. The result is a durable, low-cost system that delivers multi-speed benefits without sacrificing simplicity.
C. 3-Post Chain Configuration
Ingear’s power transfer uses a 3-post chain drive configuration: the chain wraps around three sprockets forming a triangle – the drive sprocket from the motor, the driven (morphing) sprocket at the output, and a third sprocket that functions as an idler/tensioner. This design was inspired by the efficiency of chain drives (like those in motorcycles or timing drives) but avoids the lateral chain shifting of a bicycle derailleur system. By keeping the chain on a single plane, Ingear can use a robust automotive chain (a BorgWarner HY-VO type, similar to those used in 4x4 transfer cases) which is proven to handle high torques reliably. Chain drives are actually highly efficient – the Ingear prototype’s chain is slightly more efficient than the helical gear it replaces in a traditional EV reducer. In fact, overall bench testing by a major OEM showed the Ingear transmission reaching over 99% peak efficiency , a level of minimal loss that essentially bests a single-speed gearbox. This is partly because a well-designed chain drive has very low friction – modern roller chains under proper lubrication can exceed 98% efficiency in power transfer – and partly because Ingear eliminates one of the meshing gear stages that a single-speed would otherwise use. There are no parasitic losses from multiple gear meshes being engaged at once, as can happen in multi-speed planetary transmissions, and no sliding friction “rolling” losses between gear teeth. The chain engagement is positive and rolling, with negligible slip.
The 3-post layout improves load distribution and durability. The chain wraps around a large portion of each sprocket, spreading the force over many teeth, unlike a gear mesh where typically only a couple teeth share the load at any instant. The additional contact and wrap angle provided by the tensioner sprocket means smoother force transfer and less stress per link in the chain. Furthermore, using straight-cut sprocket teeth (as opposed to helical gears) means the forces stay in the plane of the chain without generating axial (sideways) thrust. This allows the use of low-friction ball bearings instead of bulky thrust bearings , and it also avoids the efficiency loss and heat generated by sideways forces and gear sliding. In fact, because Ingear’s chain and sprockets do not create significant side loads or friction, the unit requires no dedicated oil pump for lubrication or cooling – simple splash lubrication is sufficient. This contrasts with conventional multi-speed automatics or even some single-speed reducers that need oil pumps and coolers to manage heat. By simplifying the cooling and lubrication, Ingear saves energy (no pump draw) and weight, further contributing to vehicle efficiency.
From a reliability standpoint, chain drives have come a long way – they are widely used in engines and drivelines with long life. Ingear’s chain operates in a sealed environment and stays within normal tension limits, so it doesn’t suffer from stretch or excessive wear. As noted, extensive durability testing showed no measurable chain wear after an accelerated lifetime of use. Noise is also well-controlled; straight-cut gears and chain might sound old-fashioned, but in practice a properly tensioned chain drive can run very quietly. (For instance, the Chevrolet Volt employed a chain in part of its drive system, and it remained inaudible in electric mode.) Ingear leverages these advantages: an efficient, cost-effective, and compact chain drive that replaces a bulky second gearset. By using common materials (hardened steel links and sprockets) and established manufacturing processes (the chain is off-the-shelf from a Tier-1 supplier, and the sprockets can be made with standard methods), the Ingear is truly OEM-friendly. Automakers can integrate this 2-speed unit around the existing differential with minimal re-engineering – it’s designed to fit where a single-speed reducer would fit , only adding a modest amount of mass. In return, they get a significant boost in performance and efficiency.
D. Integrated Tensioning System
A key enabler of Ingear’s smooth operation is its integrated tensioning system. The third “post” in the 3-post design is not just an idler but an active tensioner that automatically maintains the correct chain tension through all operating conditions. In the cutaway image above, this is the spring-loaded arm pushing on the chain loop. The tensioner takes up slack when the sprocket segments retract (upshift) and lets out a bit of slack when the sprocket expands (downshift), so the chain is never overly loose or tight. This prevents any lag or snatch in torque transfer during a shift – there’s no whiplash in the chain and no need for a motor torque pause to wait for engagement. By optimizing force distribution, the tensioner ensures each link and tooth carries just the right load, which prevents power loss due to slippage and eliminates excessive strain on components.
Ingear’s tensioning system is designed to react instantaneously and in concert with the shift. When an upshift or downshift occurs, the control software momentarily modulates motor torque (using a torque-fill algorithm) to make the shift ultra-smooth, while the mechanical tensioner keeps the chain perfectly taut. The result is that passengers cannot even tell a shift is happening – tests indicate shifts are imperceptible in normal driving. Even during regenerative braking, which effectively puts force through the drivetrain in reverse, the tensioner manages the chain slack so that regen can continue uninterrupted through a gear change. Many simpler two-speed setups would have to temporarily suspend regeneration or use clutches to shift, but Ingear’s system keeps regeneration continuous, including during downshifts, again thanks to the coordinated tensioner and motor control. This is a unique advantage in real-world driving: whether accelerating or decelerating, the vehicle behaves seamlessly as if it were single-speed, with the extra gear ratio only making itself known by improving efficiency and performance.
By maintaining proper chain tension and eliminating shock loads, the tensioner reduces wear and enhances durability. Fully sealed and designed to last the vehicle’s lifetime, it requires no periodic adjustment. This blend of simple mechanical design and smart software coordination exemplifies Ingear’s approach: achieving multi-speed performance with minimal complexity.
Bringing it all together:
The result is a transmission that extends range, sharpens performance, and reduces system stress—without introducing new trade-offs. Ingear maintains over 99% peak mechanical efficiency, enabling OEMs to either shrink battery size or deliver longer range at no added cost. Less heat, less waste, and smoother torque delivery make it easier to meet efficiency targets and simplify thermal management. For platforms under pressure to compete on both performance and price, Ingear unlocks meaningful gains using existing components and familiar architectures.
The Next Generation of EV Transmissions Is Already Here
The transmission problem in EVs has been solved—and it’s no longer theoretical. Ingear is already undergoing validation with major OEMs, showing measurable improvements in drivability, range, and system efficiency. It’s built from standard components, designed for mass production, and proven to work in real-world conditions. Independent testing confirms it’s the most efficient 2-speed EV transmission available today.
Unlike legacy gearbox concepts adapted from internal combustion, Ingear was built from the ground up for electric powertrains. The result: smoother torque delivery, over 99% peak mechanical efficiency, and a design that integrates cleanly into existing vehicle architectures. No rare-earth materials. No exotic manufacturing. No need for clutches, pumps, or complex controls. Just a compact, validated drivetrain upgrade that enables platform-wide cost and performance gains.
The window is open for OEMs to gain a fast follower advantage. Those who act now can unlock vehicle-level savings and performance improvements their competitors are still chasing—and send a clear signal to markets and customers that they’re building EVs for what comes next.
About Inmotive Inc.
Inmotive is a pioneering developer of ultra-efficient multi-speed powertrains for electric vehicles. The company’s flagship product, the Ingear™ transmission, delivers superior efficiency and performance for a wide range of EV applications. Committed to advancing sustainable mobility, Inmotive partners with leading manufacturers to redefine what’s possible in electric and alternative energy transportation.
How Transmissions Became A Part Of Every Car, And Why They Will Again In The EV Era
For decades, transmissions had been an unquestioned part of automotive design—until electric vehicles came along. With their instant torque and simplified drivetrains, EVs seem to operate well without the multispeed transmissions from the Internal Combustion Engine (ICE) age. However, look back at the early days of the automobile and the development of the first transmissions and you’ll see a landscape that mirrors where EVs are today.
Transmissions Shaped the Auto Industry—And Why EV OEMs Need Them.
For decades, transmissions had been an unquestioned part of automotive design—until electric vehicles came along. With their instant torque and simplified drivetrains, EVs seem to operate well without the multispeed transmissions from the Internal Combustion Engine (ICE) age. However, look back at the early days of the automobile and the development of the first transmissions and you’ll see a landscape that mirrors where EVs are today.
History has a way of repeating itself - Just as early cars first relied exclusively on brute-force engine power to achieve performance targets, today’s EVs are facing similar limitations in efficiency and performance by asking more and more from the electric motors. There comes a tipping point where the trade-offs outweigh the advantages, and we are fast approaching it. As the industry demands longer range and more cost-effective electric powertrains, mulit-speed transmissions will re-emerge as a critical piece of the puzzle. To understand why, we have to look back at how they became essential in the first place.
Early Automotive Design Philosophy
The first cars produced in the late 1800s were simplistic and low-powered. Early car builders often pursued performance by increasing engine size and power output. For example, Benz’s Patent-Motorwagen evolved from a 0.75-horsepower (HP) single-cylinder engine in 1885 to a 1.5HP version in 1887 and a 2HP model by 1888—effectively increasing engine capacity to enhance performance. This “bigger engine” approach would yield improvements to vehicle performance and capabilities , but it had limits: engines became heavier, consumed more fuel and were more expensive. As vehicles started to drive faster and carry heavier loads, it became clear that relying solely on engine size was not a sustainable solution for performance & cost.¹
The Emergence of Transmissions
Technical & commercial challenges in early cars highlighted the need for multi-ratio transmissions. Internal combustion engines have a narrow optimal RPM range for efficiency and torque, so a single fixed gear was a compromise – great for either low-speed torque or high-speed cruising, but not both. An engine geared to launch the car at grade might over-rev or waste energy at higher speeds; an engine geared for high speed would struggle to get the car moving. Early automobiles suffered in efficiency on varied terrain (e.g. climbing hills) and often required oversized engines to compensate. These challenges drove inventors to experiment with gearing.
By the 1890s, the first multi-speed transmissions appeared: The first true gearbox with multiple forward speeds was introduced in 1894 as part of the Panhard et Levassor Type A, using manually shifted gears.². This allowed drivers to change gear ratios and keep the engine in a more effective RPM range, greatly improving both performance, driveability and fuel efficiency, a big advance for the vehicle technology of the time. The trade-off was added complexity and cost, initially posing a challenge for automakers. For transmissions to be widely adopted in mass market passenger vehicles, they had to meet market-driven thresholds in three key areas:
Cost – Feasibility for mass production at competitive prices
Efficiency – Better the ratio of energy input to usable output in the drivetrain
Performance – Improved utility and capability.
1. Cost and Manufacturing Feasibility:
In the earliest years, gearboxes were expensive and complex to build. However, mass-production techniques (pioneered by Ford and others) quickly made transmissions cost-effective to manufacture and install. By the 1920s, two-speed transmissions were standard equipment even on affordable cars, indicating that the cost per unit had dropped and consumers demanded the capability. The planetary 2-speed in the Model T (1908) is a classic example of a simple, robust transmission that was cheap enough to include in a mass-market car, proving the cost hurdle could be overcome.
As designs standardized, transmissions actually saved costs – a car with a smaller engine plus a gearbox could meet performance targets more cheaply than a car that tried to use a very large engine with no gearbox. By the post-WWII era, the economies of scale made even 3- or 4-speed automatics affordable options.
2. Efficiency:
A major impetus for adding a multispeed transmission was to maximize fuel economy through having the engine spend time at its optimum state.. Early manual transmissions often employed sliding-gear designs, which required drivers to manually mesh gears. These transmissions were not synchronized, making gear shifts challenging and less efficient. In contrast, modern automatic transmissions have achieved efficiencies ranging from 86% to 94% through the shift
Each additional gear allowed the engine to run closer to its most efficient RPM over a wider range of vehicle speeds.Transmissions also enabled downsizing engines for economy: an efficient small engine with the right gearing can perform like a larger engine but use less fuel. Regulatory pressure, like those on oil and fuel efficiency in the 1970s, accelerates the transition. In this way the gearbox became a key tool for meeting regulatory requirements over the decades.
3. Performance and Drivability Gains:
For transmissions to gain widespread adoption, they had to meet usability thresholds that ensured an uninterrupted and seamless driving experience. Early transmissions often required significant driver effort, with non-synchronized gears leading to difficult shifts, noise, and excessive wear. However, as engineering improvements enabled smoother, synchronized shifts and automatic options, transmissions became effortless to use and highly reliable over long periods. Once these usability hurdles were overcome, consumers quickly embraced the added performance benefits. A more enjoyable driving experience—all without added complexity for the user. As a result, transmissions transitioned from being a mechanical necessity to a fundamental expectation in vehicle design.
The improvements were the result of engineering effort to meet these thresholds, cementing transmissions as a fundamental component of automotive design since the early 1900s.
The History of ICE Transmission Evolution
The Current State of EV Drivetrain: Big Battery, Big Motor, Single Gear
Today, electric vehicles (EVs) currently use single-speed drivetrains – typically just one fixed gear reduction between the electric motor and the wheels - Similar to the direct drives of the early ICE Age. EV designers have thus far opted to achieve the desired performance and range by using larger, more powerful, faster spinning electric motors, and sophisticated electronic control. This approach has been acceptable to the consumer since electric motors have a much wider speed range than gasoline engines. An EV motor generates peak torque from 0 rpm (launch) and sustains useful power across a broad rpm range (cruise). Automakers have found that they can cover both low-end acceleration and high-speed cruising by selecting an appropriate single gear ratio and then using a motor (or multiple motors) potent enough to deliver on both ends. The industry’s design philosophy so far has therefore been to keep the drivetrain mechanically simple (one gear) and rely on the motor’s flexibility and managing the associated motor complexity
But it hasn’t always been this way. In fact, Tesla’s early experience with the original 2008 Tesla is demonstrative of the challenges of using ICE-age transmissions in EVs. The Tesla Roadster attempted to use a legacy 2-speed transmission to meet its ambitious acceleration and top speed targets. However, the conventional ICE-age gearbox could not handle the high torque and failed in testing, forcing Tesla to abandon it. This transmission couldn’t meet the cost, efficiency, or performance thresholds needed for transmissions to be successful in this new generation of vehicle. Electric motors had changed the game.
Tesla’s solution was to drop the transmission entirely and go with a single-speed, compensating by upgrading to a more powerful motor to hit the performance goals.³ This set the tone for many EVs to come. Manufacturers have, so far, been willing to tolerate the complexity, weight and cost increase of a larger motor in exchange for the mechanical simplicity of a single-speed drivetrain. This is due, in part, to the perception that the complexity, weight and cost of today’s modern transmission is not the most effective way to meet the vehicle requirements. The paradigm to today is to iterate on the motor
EVs suffer from the Inherent Limitations of Single-Speed Drives
The one-gear approach works in a price-insensitive EV marketplace, but it isn’t without compromises. Single-speed setups can push the electric motor out of its ideal efficiency zone, just like the internal combustion engines of the past. At high highway speeds, the motor can spin at a high RPM where its efficiency drops off, wasting energy as heat. Likewise, at very low speeds or heavy loads (towing, steep grades), a single gear might force the motor to draw huge currents to produce the needed wheel torque. Using a single fixed gear ratio means EV designers must make a trade-off between acceleration (torque) and top speed and include excess battery capacity to offset the losses.
Automakers try to find an optimal middle ground, and powerful motors help mask the compromise – but the underlying limitation remains. As Mate Rimac (designer of the Rimac Concept One electric hypercar) explained, “in electric cars you normally need to decide between acceleration or top speed when you have a single-speed gearbox”.⁴
Academic and industry research backs up these examples. Multiple studies have investigated two-speed or multi-speed EV transmissions. For instance, a 2015 simulation study by Zhang et al. found that adding a two-speed gearbox to an EV could reduce energy consumption by ~6.6% and increase driving range by ~7% compared to a single-speed drive.⁵ In general, literature suggests a meaningful efficiency gain on the order of 5–10% with addition of a 2-speed transmission, as well as the ability to use a smaller motor for the same performance.
Product Planners: What could you do with 5-10% more range from the same battery pack?
So Why Haven’t We Seen A Proliferation Of Multispeed Transmissions In EVs?
These efficiency improvements translate into extended range or the possibility of using a smaller battery pack for the same range, which in an industry obsessed with squeezing out every extra mile, is significant. Such findings are spurring continued R&D – evidenced by many patents being filed for multi-speed EV transmission designs. In fact, an analysis by GlobalData found over 120 companies, from startups to major automakers, are actively working on two-speed EV transmission innovations, indicating broad interest in this area. Major carmakers like Hyundai, Mercedes-Benz, and Toyota are among the top patent filers, aiming to enhance acceleration and high-speed efficiency with multi-gear systems in their future EVs.⁶
Why have we seen so few of these make it to market? To date, manufacturers have tried to use ICE-age transmission designs and techniques in EVs to reap the benefits of multi gear setups. These efforts have met challenges, because EVs increased the thresholds in each of the 3 areas:
Cost – EVs drivetrains are simpler and lower cost than their ICE counterparts. EV Transmissions must be compact and ready for mass production at ultra low costs
Efficiency – Due to range anxiety and battery charge times, EV drivetrains demand higher efficiency compared to their ICE counterparts - EV Transmissions must be >97% efficient to add value to the vehicle
Performance – EV fixed-ratio drivetrains are smoother and more powerful than their ICE counterparts. To compete in EVs, multi-speed transmissions must deliver imperceptible shifts with no gaps in torque delivery. However, the high torque and extended RPM range of electric motors place new durability demands on gear design. At the same time, the bar for noise, vibration, and harshness (NVH) is even higher, requiring transmission solutions that enhance performance without compromising refinement.
Conventional ICE-age transmission designs have not met the evolving demands of EVs in these areas. They tend to be costlier, less efficient, and struggle to deliver the seamless shifts required for EV applications. However,If history is any guide, the trajectory of EV drivetrains will eventually mirror that of ICE vehicles in embracing multi-speed transmissions that exceed the market thresholds in all 3 of these areas. To achieve this, invention is required.
That’s why Inmotive conceived a 2-speed transmission that’s fundamentally different - the Ingear is the first example of a transmission that meets the EV demands in all 3 of these categories simultaneously. Our patented technology is similar in costs to a fixed gear drive, operates at >99% efficiency, and has an imperceptible shift with continuous power delivery.
The Road Ahead
In an era where EV manufacturers are engaged in aggressive cost competition, the ability for OEMs to meet performance targets at a lower cost will become a defining factor in market differentiation. Just as multi-speed transmissions allowed smaller, more efficient internal combustion engines to outperform larger, fuel-hungry alternatives, applying similar principles to EVs enables automakers to achieve strong acceleration and range while reducing reliance on expensive components like the geopolitically risky high-capacity batteries, oversized rare-earth motors, and supply-chain challenged chips and power electronics.
By optimizing power delivery through gearing, manufacturers can extract more performance from smaller motors and extend range without adding battery. OEMs who do adopt will see lower production expenses and enhanced vehicle efficiency, creating a clear divide in the EV market between cost-effective, high-performing models and those that remain constrained by the inherent limitations of single-speed drives.
The story of transmissions is one of necessity, innovation, and eventual ubiquity. Historically, they unlocked efficiency, performance, and cost advantages for combustion engines, shaping the trajectory of automotive design. Now, as EVs dominate the future, the same fundamental forces are at play. The industry’s early skepticism toward multi-speed transmissions in EVs mirrors past resistance to technological shifts—but as history has shown, efficiency, cost, performance advantages ultimately drive adoption. With automakers seeking new ways to differentiate on cost, range, and power delivery, the case for multi-speed EV transmissions is only growing stronger.
Just as they once transformed ICE vehicles, transmissions will once again prove inevitable in shaping the next generation of electric mobility.
About Inmotive Inc.
Inmotive is a pioneering developer of ultra-efficient multi-speed powertrains for electric vehicles. The company’s flagship product, the Ingear™ transmission, delivers superior efficiency and performance for a wide range of EV applications. Committed to advancing sustainable mobility, Inmotive partners with leading manufacturers to redefine what’s possible in electric and alternative energy transportation.